Mining explosion-proof lamps are designed with specific materials and coatings to enhance their durability and resistance in challenging mining environments. The choice of materials is crucial to ensure the lamps can withstand various hazards commonly found in mining operations, including dust, moisture, mechanical stress, and potential exposure to explosive gases. Here are some common materials and coatings used:
Corrosion-Resistant Materials:
The exterior housing of mining explosion-proof lamps is often made from corrosion-resistant materials such as stainless steel or aluminum alloys. These materials help prevent corrosion, ensuring the longevity of the lamp in harsh mining conditions.
Impact-Resistant Casings:
The lamp housing may be reinforced with impact-resistant materials, such as rugged polymers or rubberized coatings, to withstand mechanical stress and potential impacts in the mining environment.
Sealed and Gasketed Enclosures:
Mining lamps are typically designed with sealed and gasketed enclosures to prevent the ingress of dust and moisture. This feature helps maintain the integrity of the lamp's internal components and protects against environmental hazards.
Anti-Static Coatings:
Anti-static coatings may be applied to the lamp's surface to reduce the risk of static electricity buildup. This is particularly important in mining environments where combustible dust or gases may be present.
Heat-Resistant Components:
Internal components of the lamp, including wiring and insulation, may be designed to be heat-resistant to ensure safe operation even in high-temperature environments. Heat-resistant materials help prevent malfunctions and maintain the lamp's performance.
UV-Resistant Materials:
UV-resistant coatings or materials may be used to protect the lamp's exterior from the effects of prolonged exposure to sunlight, which can degrade certain materials over time.
Chemical-Resistant Finishes:
In environments where exposure to chemicals is a concern, mining lamps may feature chemical-resistant finishes or coatings to prevent degradation and maintain the lamp's structural integrity.
Powder Coating:
Powder coating is a common method used to apply a durable and protective finish to the lamp's surface. It helps resist scratches, chips, and environmental wear.
IP Ratings:
Mining lamps often carry specific Ingress Protection (IP) ratings, indicating the degree of protection against solid particles (like dust) and liquids (such as water). Higher IP ratings signify greater protection.
UV Stabilizers:
UV stabilizers may be incorporated into the materials or coatings to prevent the degradation of the lamp's exterior due to exposure to ultraviolet (UV) radiation.
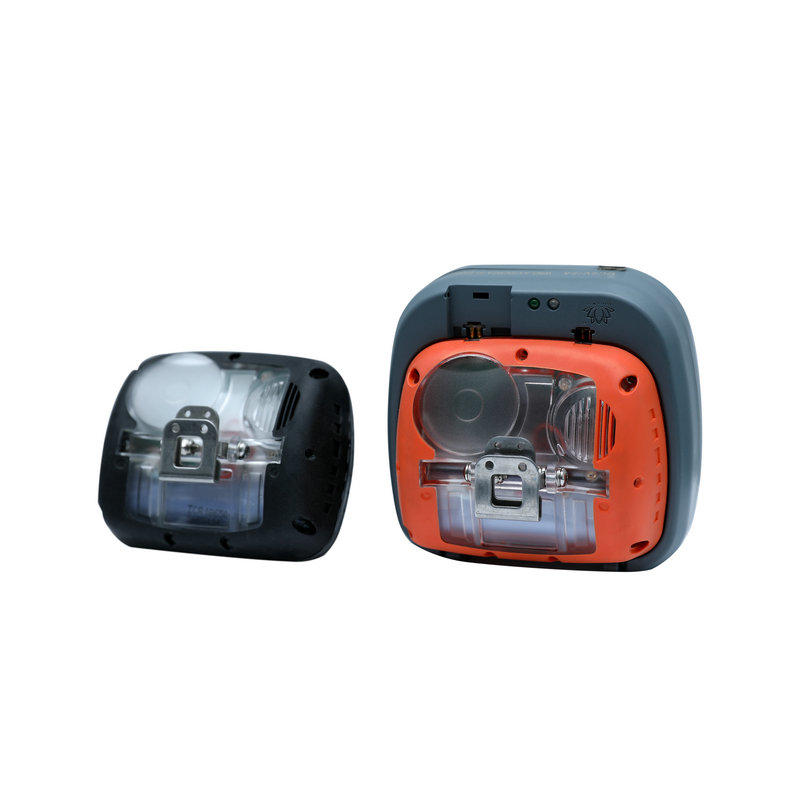